Can the technology that lowers e.t. improve your profitability?

by Matt Hartford, NHRA Pro Stock Driver & CEO of Total Seal Piston Rings, and Lake Speed Jr., Certified Lubrication Specialist
As racers, we know improving mechanical efficiency – reducing friction and drag – improves e.t. We can see it on the time slip. What if you could see improved mechanical efficiency on your financial reports?
Engines that consume less fuel and compressors that draw less current would save a company on fuel and energy costs over time, especially with today’s fuel costs.
Engines and compressors that last longer obviously save money by reducing replacement/rebuild costs.
Engines with less blowby enable longer engine oil life, which can save money through fewer oil changes (both in labor and oil costs).
With inflation driving up the cost of materials and labor, isn’t now the best time to look for areas to improve efficiency?
Well, the No. 1 source of friction and wear in engines are the piston rings rubbing against the cylinder walls. That’s why NHRA Pro Stock engines, the most efficient naturally aspirated engines in the world, use the thinnest piston rings – improved mechanical efficiency.
Multiple research studies from Ford and the U.S. Department of Energy have concluded that the piston ring and cylinder wall account for as much as 40% of all engine friction. No wonder today’s OEM engines have thinner pistons rings than their predecessors.
Think about that ’72 Camaro and its 350 CI small-block, which had 5/64, 5/64, 3/16 rings. Now think about the LS7 with its 1.2mm, 1.2mm, 3.0mm rings – that’s a 40% reduction in ring size!
As racers, we think of thinner rings providing more horsepower. As businesspeople, we need to think of piston rings as providing more profit.
Let me give you an example.
In a recent test at Shaver Specialties Racing Engines, the effects of ring size and tension on engine horsepower and operating temperature was measured.
The base line for this test was a set of Total Seal Diamond Finish .7mm, .7mm, 2.0mm rings, which is 55% thinner than a 1/16th, 1/16th, 3/16th package. The engine was run at 2,800 rpm with a fixed load setting of 75 foot-pounds and a fixed coolant flow setting. At the end of 30 minutes, three consecutive dyno sweep tests (3,000 rpm to 6,000 rpm) were performed. At the end of those three tests, both water temperature and oil temperature were recorded.
The engine was then fitted with a standard set of 1/16th-inch, 1/16th-inch, and 3/16th-inch rings. Again, the engine was run at 2,800 rpm with a fixed load setting of 75 foot-pounds and a fixed coolant flow setting. At the end of 30 minutes, three consecutive dyno sweep tests (3,000 rpm to 6,000 rpm) were performed. At the end of those three tests, both water temperature and oil temperature were recorded.
Two different tests with the 1/16th, 1/16th, 3/16th rings generated about 15 degrees hotter water temperature and nearly 20 degrees hotter oil temperature compared to the .7mm, .7mm, 2mm ring set.
This is significant because the operating life of engine oil is cut in half with every 20 degrees Fahrenheit increase in operating temperature. Imagine the savings in labor and material costs if you could double the oil service life in your business’s engines and compressors!
These results confirm piston ring to cylinder wall friction as a meaningful contributor to engine operating temperature, and identifying friction as the source of the heat was quite easy. The standard 1/16th, 1/16th, 3/16th rings reduced engine power by nearly 20 foot-pounds of torque and more than 15 hp compared to the gas-ported .7mm, .7mm, 2mm ring set. In fact, the 1/16th, 1/16th, 3/16th ring set generated so much oil temperature that the label on the oil filter began to “shrink” from the heat!
If the thinner rings had simply trapped the combustion heat in the piston, then we would not have seen a decrease in oil temperature with the thinner rings. In fact, we would have seen the opposite – the oil temperature would have increased. Because both the water and oil temperatures dropped, we can determine with certainty that the temperature reduction came from reduced friction.
We already know that reducing friction increases efficiency, and those horsepower improvements can also yield significant cost savings.
In racing, we want to go as fast as possible, so we crave more horsepower. In business, we can elect to run faster (get the job done quicker) or to operate at the same pace (but more efficiently, less waste).
This is where the benefits of advanced piston ring technology really kick in. By reducing friction, fuel and energy savings can be realized.
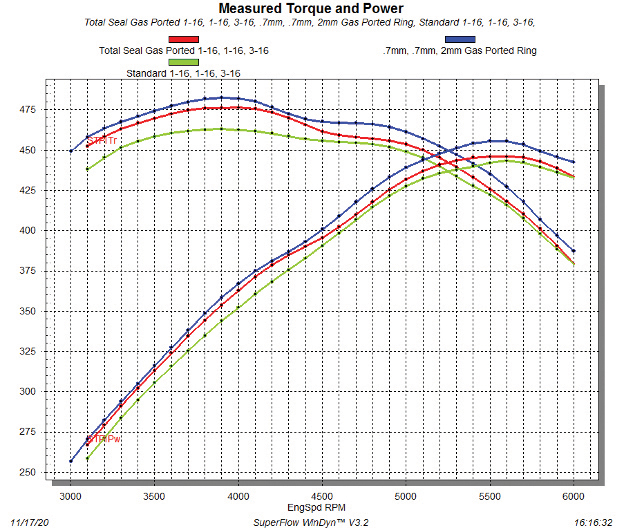
Increased horsepower equals increased efficiency, so a 3% increase in efficiency can yield either more horsepower (455 hp vs. 440 hp) or less fuel consumption to hit a target speed. How much is 3% of your annual fuel costs?
Does this fuel economy come at a cost in durability? The answer is: No. Back to the test at Shaver’s, used oil samples were taken from each test cycle and analyzed by an independent lab. Those results revealed a 55% reduction in wear by going to the thinner rings. Interestingly, the .7mm rings are 55% thinner than the 1/16th rings, so there is a direct correlation in ring thickness to wear.
Let’s go back the car manufacturers; they’ve gone from thicker, cast iron rings to thinner, steel rings over the last several decades. Why? To improve fuel economy, but today’s engines also last much longer than before.
A recent presentation by Gehring at a global engineering conference revealed that typical production engines from the U.S. “Big Three” in the ’70s and ’80s lasted about 50,000 to 70,000 before the cylinders were worn out. Today, those companies produce engines that live 150,000 to 200,000 miles before the cylinders are worn out. Again, today’s production engines utilize thinner, lower tension, steel piston rings.
The evidence clearly shows that more efficient piston rings increase horsepower, reduce engine temperature (both water temperature and oil temperature), and the reduction in operating temperature also extends motor oil life. These positive effects increase engine life and reduce operating costs.
But is there more to be gained beyond just thinner piston rings?
Our Gapless® piston rings consistently demonstrate improved efficiency in both diesel engines and compressors. In fact, some of our largest customers for the Gapless® piston rings don’t build race engines, and many of the technologies born from racing apply to stationary engines for industrial use, OTR diesel trucks, and everything in between.
Our latest patented technology adds gas porting to the piston ring instead of the piston, which reduces blowby without increasing cylinder bore wear.
Gas-ported pistons are not new. The practice of drilling holes (ports) into pistons to allow the gas pressure above the piston to get behind the top piston ring, which helps seal the ring against the ring groove and cylinder wall, has been around at least since the 1970s. What is new are gas-ported piston rings. Instead of drilling holes into the piston, slots are cut into the piston ring. Both gas-ported pistons and gas-ported rings allow more gas pressure above the piston to get into the ring groove an exert outward and downward force on the piston ring itself.
Accordingly, the better the rings seal against the cylinder wall, the less combustion blowby gas pressure can reach the crankcase. When a piston ring doesn’t seal well against the piston ring groove and cylinder wall, the gas pressure above the piston leaks past the piston ring, which pressurizes the crankcase of the engine. So, blowby can be quantified by measuring crankcase pressure.
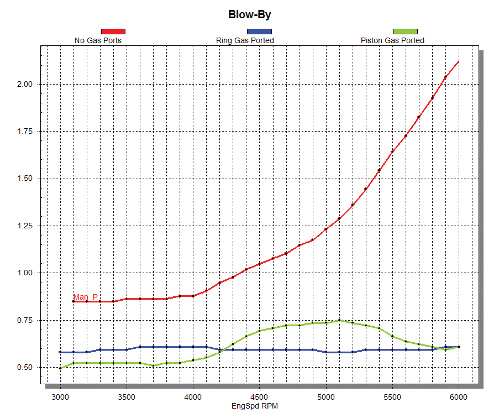
As the test results clearly reveal, gas-ported piston rings greatly reduce blowby, and blowby is the No. 1 enemy of your motor oil. High levels of blowby increase oil temperature and contamination, which reduce the service life of the oil. Accordingly, reducing blowby is the key extending oil service life, which pays substantial dividends in cost savings. Imagine cutting your routine engine maintenance costs in half. What would that do to your operating expenses?
All of this might sound impossible, but we see customers improving efficiency and durability every single day by applying the same engineering principles used in Pro Stock racing – sometimes they are just using them for a different purpose. In the end, the results are the same – increased efficiency.
No matter what the application, an engineered piston ring package can unlock the performance potential of any engine or compressor. If you are interested in improving the EBITDA [Earnings Before Interest, Taxes, Depreciation, and Amortization] of your business, think about piston rings. They help my Pro Stock car go faster, and they can help your bottom line.